空气搅拌铝合金钝化槽液对钝化成膜的影响有哪些
点击次数:382
发布时间:2025-04-28
空气搅拌在铝合金钝化处理中对钝化成膜的影响是多方面的,既有积极作用也有潜在风险。以下是具体分析:
1. 槽液均匀性
正面影响:空气搅拌可防止钝化液成分沉淀,确保槽液中化学物质(如钝化剂、酸/碱、添加剂)分布均匀,从而促进铝合金表面成膜的一致性,减少色差或厚度不均。
负面影响:若搅拌不均匀,可能导致局部浓度差异,影响钝化膜质量。
2. 氧气参与反应
促进氧化:搅拌引入的氧气可能加速铝合金表面氧化反应,尤其对依赖氧化成膜的钝化液(如铬酸盐体系),可能提高膜层致密度和耐蚀性。
成分氧化风险:某些钝化液成分可能因氧气过多被氧化分解,需根据配方调整搅拌强度。
3. 反应速率与膜层结构
加速反应:搅拌增强传质效率,缩短成膜时间,但需控制避免反应过快导致膜层疏松或多孔。
优化结构:适度搅拌可形成更均匀致密的膜层,但过度搅拌可能破坏成膜过程稳定性。
4. 气泡与膜层缺陷
气泡附着:搅拌产生的气泡若附着在工件表面,可能导致局部钝化不良,形成点蚀或膜层不连续。
对策:优化搅拌位置(如槽体侧方)或采用间歇搅拌,减少气泡接触工件。
5. 机械冲刷作用
潜在损伤:强搅拌可能导致已形成的钝化膜被冲刷剥离,尤其是处理后期膜层较薄时。
控制参数:需根据钝化阶段调整搅拌强度,初始阶段可较强,后期减弱。
6. 温度与稳定性
热效应:搅拌可能导致槽液温度升高(尤其大容量槽体),需配合温控系统维持最佳反应温度(通常20-40℃)。
挥发控制:搅拌可能加速钝化液中易挥发成分(如酸性物质)的损失,需定期监测浓度并补充。
7. 钝化液寿命
延长寿命:均匀搅拌可减少局部成分消耗不均,延长槽液使用寿命。
成分降解:过度搅拌可能加速某些成分(如有机添加剂)的降解,需根据配方评估。
优化建议
参数匹配:根据钝化液类型(铬系/无铬)、浓度及工艺要求,选择低压弱搅拌(如0.1-0.3 MPa气压)或间歇式搅拌。
设备设计:采用分散均匀的气石或管道布局,避免气泡直接冲击工件。
工艺验证:通过赫尔槽试验或小试确定最佳搅拌强度和时间,结合膜层检测(如SEM观察形貌、电化学测试耐蚀性)。
总结
空气搅拌在铝合金钝化中是一把“双刃剑”,合理运用可提升膜层均匀性和效率,但需警惕气泡干扰和机械损伤。实际应用中需通过实验优化参数,平衡搅拌的利弊,以实现高质量的钝化膜层。
右边搅拌导致的不均匀:
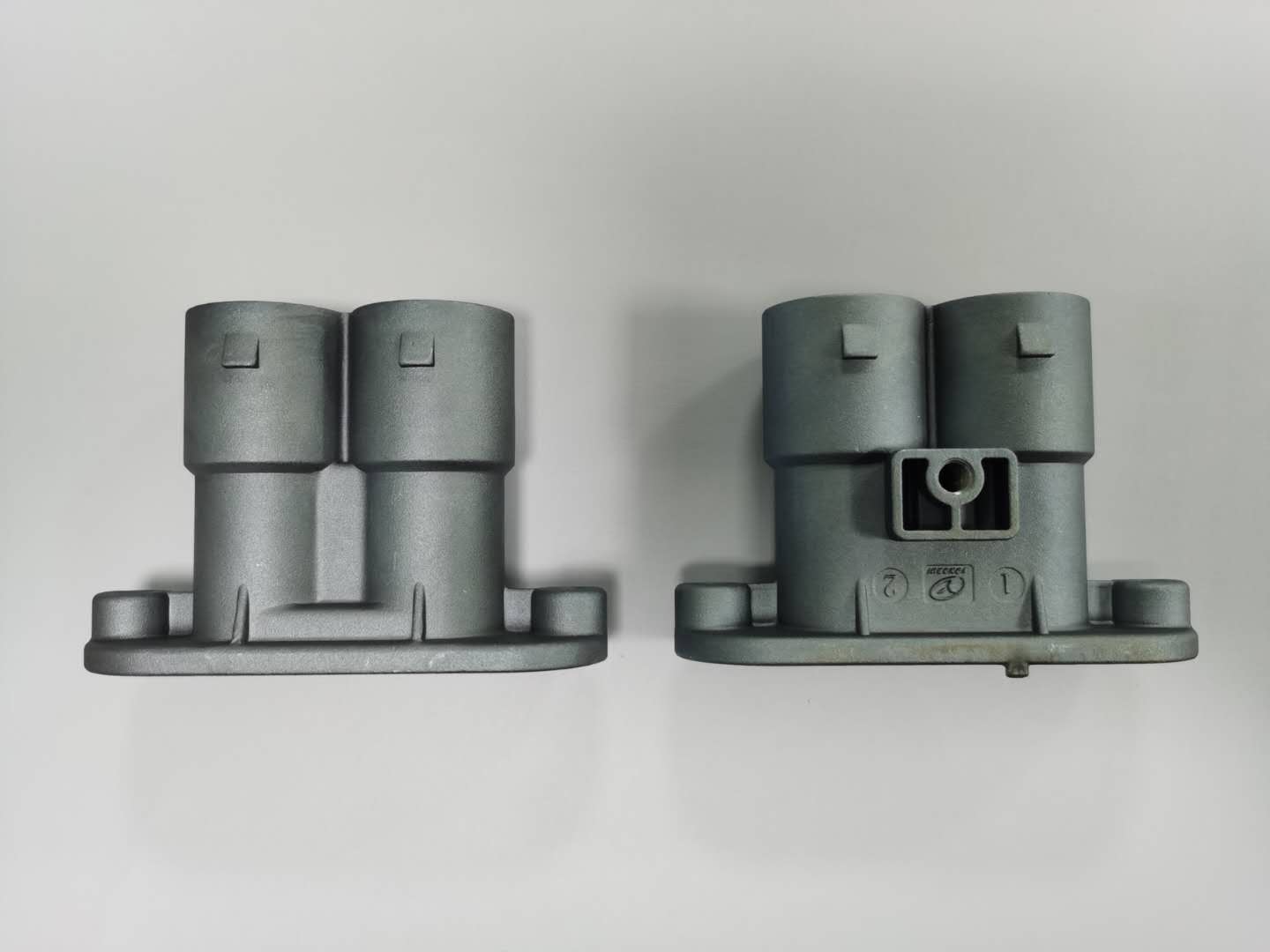